Robotics in Manufacturing: The Future’s Here and It’s Wild
Explore how robotics is revolutionizing manufacturing with increased efficiency, safety, and productivity while addressing the challenges of integration.
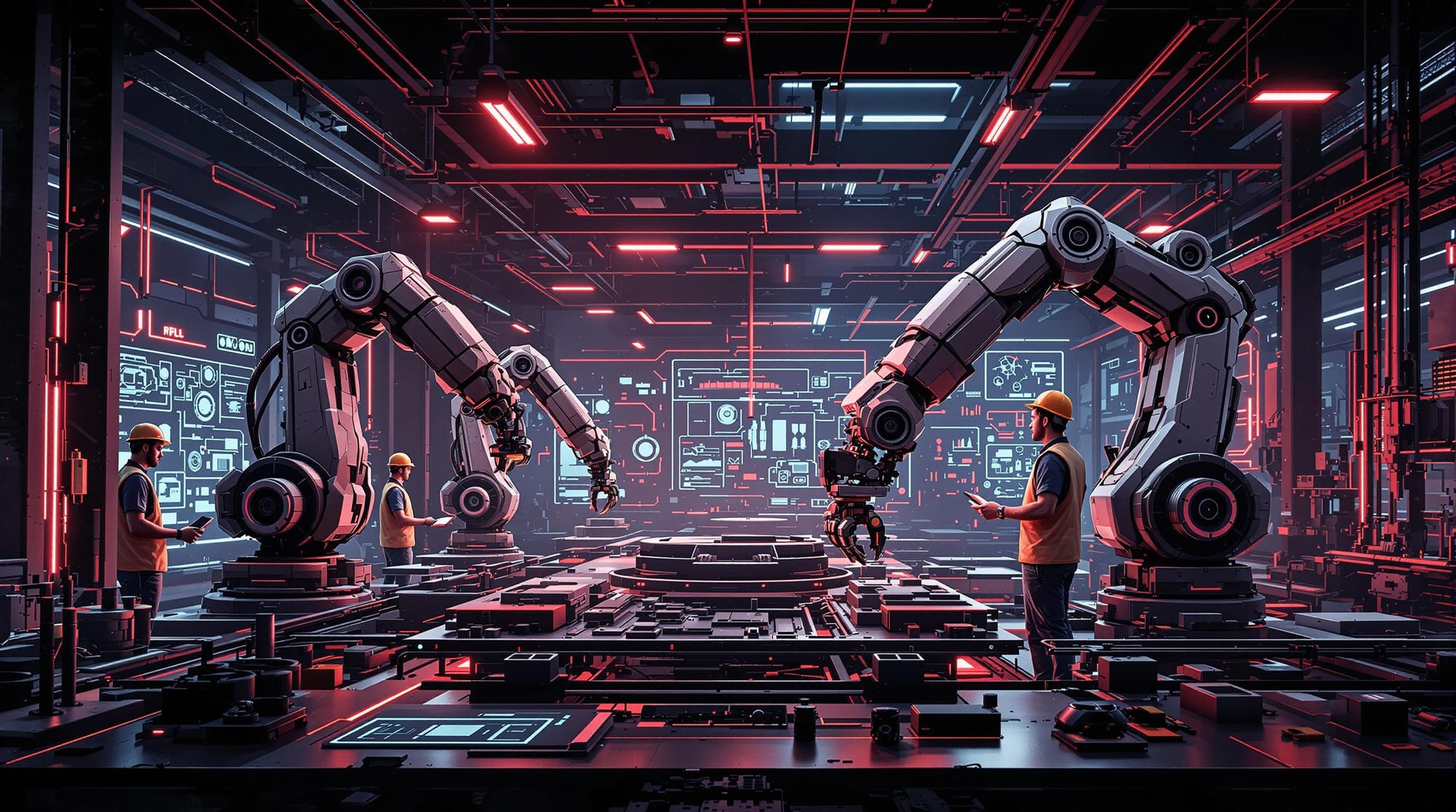
Manufacturing is changing fast. Over 500,000 robots were installed globally in 2022; by 2024, that number is expected to reach 600,000. Robots are transforming factories into high-speed, precise, and safer workplaces. Here’s what you need to know:
- Key Robot Types: Collaborative robots (Cobots) work with humans, autonomous mobile robots (AMRs) handle materials, and AI-powered systems improve quality and efficiency.
- Big Benefits: Faster production, 24/7 operations, fewer workplace injuries, and better product quality.
- Real-World Impact: Nestlé boosted productivity by 53% with robots, and the U.S. Air Force cut jet-painting labor hours by 81%.
- Challenges: High setup costs, cybersecurity risks, and the need for skilled workers.
Packaging Automation Trends in 2023
Main Robot Types in Manufacturing
Manufacturing today relies heavily on three main types of robots, each playing a crucial role in modern production processes.
Collaborative Robots (Cobots)
Cobots are changing the game in automation by working side-by-side with human workers - no safety cages required. These robots are designed to interact directly with people, making them safer and easier to program. They’re also a cost-efficient option for many manufacturers.
The market for cobots is booming. In 2022, it was valued at $1.4 billion and is expected to skyrocket to $27.4 billion by 2032, growing at an annual rate of 36.3% [3]. Companies like BMW and Ford use cobots for gluing, welding, and quality inspections, while Procter & Gamble employs them for precise assembly and packaging [3]. This blend of human and robotic effort is reshaping how factories operate.
Autonomous Mobile Robots (AMRs)
AMRs take automation a step further by revolutionizing material handling in manufacturing. These robots can move materials and components through facilities without human guidance, making them ideal for automating repetitive tasks.
What sets AMRs apart? They can:
- Navigate complex factory layouts on their own
- Safely handle heavy materials
- Operate nonstop during peak production times
- Minimize risks tied to manual material handling
By automating these processes, AMRs help streamline workflows and reduce workplace injuries [2].
AI-Powered Robot Systems
AI is pushing manufacturing robots to new levels of precision and efficiency. The AI Robots Market, valued at $15.2 billion in 2023, reflects the growing demand for smarter automation [4].
Companies like GrayMatter Robotics and Veo Robotics are at the forefront of this shift. Veo Robotics, for example, combines 3D sensing, computer vision, and AI to create safer work environments without sacrificing productivity [5].
"What if existing manufacturing and large technological innovations came together to create the next big manufacturing reinvention? This is the fourth manufacturing revolution, and it's happening right now" [5].
AI-powered robots are particularly effective in:
- Predictive maintenance
- Automating quality control
- Real-time production adjustments
- Learning and adapting to new tasks
Together, cobots, AMRs, and AI-powered systems are reshaping manufacturing. They’re making factories more efficient, safer, and better equipped to handle the demands of modern production.
Key Advantages of Manufacturing Robots
Production Speed and Accuracy
Robots have transformed production processes with unmatched speed and precision. For example, in electronics manufacturing, pick-and-place robots can install 30,000 components per hour on circuit boards with microscopic accuracy [1]. This level of efficiency is far beyond what manual labor can achieve. Similarly, in the automotive industry, robotic systems complete entire welding cycles in just 85 seconds, ensuring consistent quality across thousands of units [1].
Non-Stop Production Capability
Robots also make 24/7 production a reality. Unlike human workers, robots don’t need breaks, allowing continuous operation. A great example is the Philips Electric Razor Plant in the Netherlands, which uses 128 robots and nine quality assurance employees to maintain uninterrupted production [1]. This setup increases output and ensures consistent product quality across all shifts.
Workplace Safety Improvements
Integrating robots into manufacturing has made workplaces safer. Studies show that increasing robot density by 1.34 robots per 1,000 workers reduces work-related injuries by about 1.2 per 100 full-time workers, saving an estimated $1.69 billion annually in injury costs [7].
"Recent advancements in data science and artificial intelligence mean that robotic vehicles and arms aren't just capable of augmenting complex, precise tasks alongside human workers, but in many instances can eliminate employees' exposure to dangerous machinery and workplace hazards altogether." - Katherine Mendoza, senior director, workplace programs, NSC [7]
Robots contribute to workplace safety in several ways:
- Heavy lifting: They minimize the risks of musculoskeletal injuries from manual material handling [6].
- Hazardous tasks: Automated systems reduce worker exposure to dangers like cutting and welding [6].
- Noise reduction: Isolated robot operations lower workers' exposure to excessive noise levels [6].
The adoption of robotics in manufacturing is growing fast. In 2022 alone, installations increased by 12%, adding 41,624 units to North American manufacturing facilities [6].
Industry-Specific Robot Applications
Robots are transforming industries by solving specific challenges and improving operational efficiency across various sectors.
Look at The Lee Company’s automation facility in Westbrook, Connecticut, USA. You’ll see how humans work with automation equipment and robots to maintain the highest-quality components.
Auto Manufacturing Systems
The automotive industry has become a leader in using robotics. For example, Ford employs more than 100 cobots across 24 global plants, revolutionizing assembly lines. These robots are particularly good at tasks like painting with consistent coverage and conducting quality inspections using advanced sensors.
BMW and Mercedes-Benz have also improved production processes with robotics. At Mercedes-Benz, cobots manage intricate wiring installations and can adapt to quick configuration changes [8]. Tesla showcases how versatile robotics can be, with cobots that easily shift from installing battery packs to performing final quality checks [8].
The electronics industry is another area where robotics is crucial, particularly for precision and logistics.
Electronics Production
Precision and cleanliness are critical in electronics manufacturing, and robots are stepping up to meet these demands. KNAPP's Open Shuttles, for instance, are autonomous mobile robots that optimize internal logistics by handling loads efficiently and adjusting automatically.
The adoption of robotics in this sector has been remarkable. By 2021, 60% of electronics manufacturers had implemented autonomous mobile robots (AMRs), and this number is expected to reach 90% by 2024 [9]. This shift is driven by the fact that 81% of manufacturers report needing improvements in their supply chains [9].
Aerospace Manufacturing
Robots are also addressing the unique challenges of aerospace manufacturing, where complex assembly processes are the norm. For example, assembling a Boeing 777 involves over 60,000 rivets [10]. Spirit AeroSystems has used robotics to cut quality control inspection times for large composite parts by 40% [11].
The aerospace industry is also grappling with workforce shortages. According to the Welding Society, nearly 400,000 welding jobs in the U.S. could go unfilled by 2024 [10]. Robots are helping to bridge this gap by:
- Reducing washing times by 95% [10]
- Taking on hazardous tasks
- Supporting digital workflows
- Inspecting hard-to-reach areas
These advancements increase productivity and allow human workers to focus on more specialized roles.
"Robot manufacturers and integrators are shaking up a number of industries in their own ways. The aerospace industry is certainly no different." – Purkhet Abderyim, Spatial NAM Sales Director [11]
Working with Robots
Manufacturing workers need technical know-how and interpersonal skills to effectively work alongside robots. Key areas of expertise include mathematics, programming, problem-solving, and systems thinking.
Training programs typically emphasize three main areas:
- Operating and programming robots
- Following safety guidelines for human-robot collaboration
- Performing maintenance and troubleshooting tasks
For example, Universal Technical Institute (UTI) offers an 18-month Robotics and Automation Technician program. This program covers topics like 3D printing, computer-aided design, and programmable logic controllers, equipping students for entry-level roles.
Robot-Related Job Positions
With these skills, new and better-paying roles in robotics are becoming available:
- Entry-Level: Robotics Technician/Operator – approximately $66K (requires a high school diploma, GED, or certification)
- Intermediate: Robotics Specialist/Engineer – approximately $105K (requires a four-year degree)
- Advanced: Robotics Integrator – approximately $127K (requires an advanced degree or significant experience)
These roles offer salaries about 30% higher than traditional entry-level manufacturing positions. Over the next decade, an estimated 4.6 million manufacturing jobs must be filled [14].
Human-Robot Teamwork
Advanced training and specialized job roles facilitate effective collaboration between humans and robots on production floors. For instance, Siemens' Bad Neustadt facility uses the LBR iiwa lightweight cobot to handle repetitive tasks, allowing workers to focus on more complex decision-making [13]. In the automotive sector, 83% of production units now involve shared human-robot assembly tasks [12].
This collaboration boosts efficiency and reduces manufacturing costs by 20% to 60% [15]. Additional benefits include better workplace ergonomics, improved production adaptability, and enhanced quality control. Success hinges on clear communication, well-defined roles, and thorough training.
"What if existing manufacturing and large technological innovations came together to create the next big manufacturing reinvention? This is the fourth manufacturing revolution, and it's happening right now" [5].
These developments highlight the industry's shift toward an integrated, high-performance future.
Current Limitations and Future Outlook
Setup Costs and Technical Issues
Switching to robotic manufacturing can be expensive and technically challenging. These systems require significant initial investments and specialized integration, often leading to technical hurdles. Dedicated maintenance and technical support are essential to address these challenges [16].
Manufacturers are tackling these issues with three main strategies:
- Pilot Projects: Starting with small-scale trials to prove value before committing to full-scale deployment.
- Alternative Financing: Using models like Robot-as-a-Service (RaaS) to reduce upfront costs.
- Strategic Partnerships: Working with educational institutions to ensure a steady flow of skilled workers.
However, financial and technical challenges aren't the only concerns - security has become a major issue.
Security Concerns
Cybersecurity is a critical focus in connected manufacturing environments. The sector is particularly at risk, with one in five companies reporting cyberattacks [18].
"A risk assessment should consider potential threats and vulnerabilities to gauge the likelihood of a successful cyberattack." – Hal Thomas, Cybersecurity Consultant [18]
To safeguard robotic systems, manufacturers need to implement robust security measures, including:
- Access Control: Using multi-factor authentication and following the principle of least privilege.
- Network Security: Separating robot networks from traditional IT infrastructure.
- Software Management: Regularly updating security patches and firmware.
- Employee Training: Providing ongoing cybersecurity education for staff.
While addressing these risks is crucial, the industry is already considering new advancements.
Next-Generation Manufacturing
With rapid technological advancements, the global robotics market is projected to grow from $46 billion to $169.8 billion by 2032 [19]. Key developments in the field are driving this growth.
In 2023, the U.S. installed 39,000 industrial robots - a 10% increase in robot density to 228 per 10,000 employees. Improvements in cobot safety and user-friendly interfaces have further contributed to this growth [20].
"Automation is the golden key to industrial progress. But with great power comes great responsibility." – Jonathan Selby, General Manager; Technology Practice Lead [17]
Robots are also important in promoting eco-friendly manufacturing by reducing material waste and increasing production efficiency [21]. Beyond traditional factories, industries like food processing, agriculture, and construction are now adopting robotic technologies [20]. These advancements will push the boundaries of speed, accuracy, and safety across various sectors.
Robot Powered Human Strategy
The rise of robotics in manufacturing is driving faster and smarter production processes. According to an MIT study, integrating robots with human workers can cut idle time by 85% [22]. Current advancements also reveal that 64% of manufacturing tasks can be automated [23]. These numbers highlight the ongoing transformation happening on factory floors.
Take BMW's Spartanburg plant as an example. Universal Robots collaborate with human workers to apply protective foil over door electronics. This approach not only addresses ergonomic concerns but also maintains production flexibility. Richard Morris, vice president of assembly at the Spartanburg plant, put it perfectly:
"Ideas come from people, and a robot is never going to replace that" [24].
This shift enhances workers' roles rather than replacing them. With projections of 2.1 million unfilled manufacturing jobs by 2030, the demand for skilled human expertise in an automated world is clear [25]. This collaborative approach demonstrates how technology can complement human abilities rather than compete with them.
A smart strategy combining automation and human skills is key to making this work. By 2027, automation is expected to make up 25% of capital spending [26]. Torsten Franz pointed out that modern systems allow workers to step in as needed without being limited by traditional safety barriers [13]. This flexibility shapes a future where humans and machines work better together.