How to Optimize Manufacturing Processes with AI
Explore how AI is transforming aerospace and defense manufacturing by enhancing production efficiency, quality control, and supply chain management.
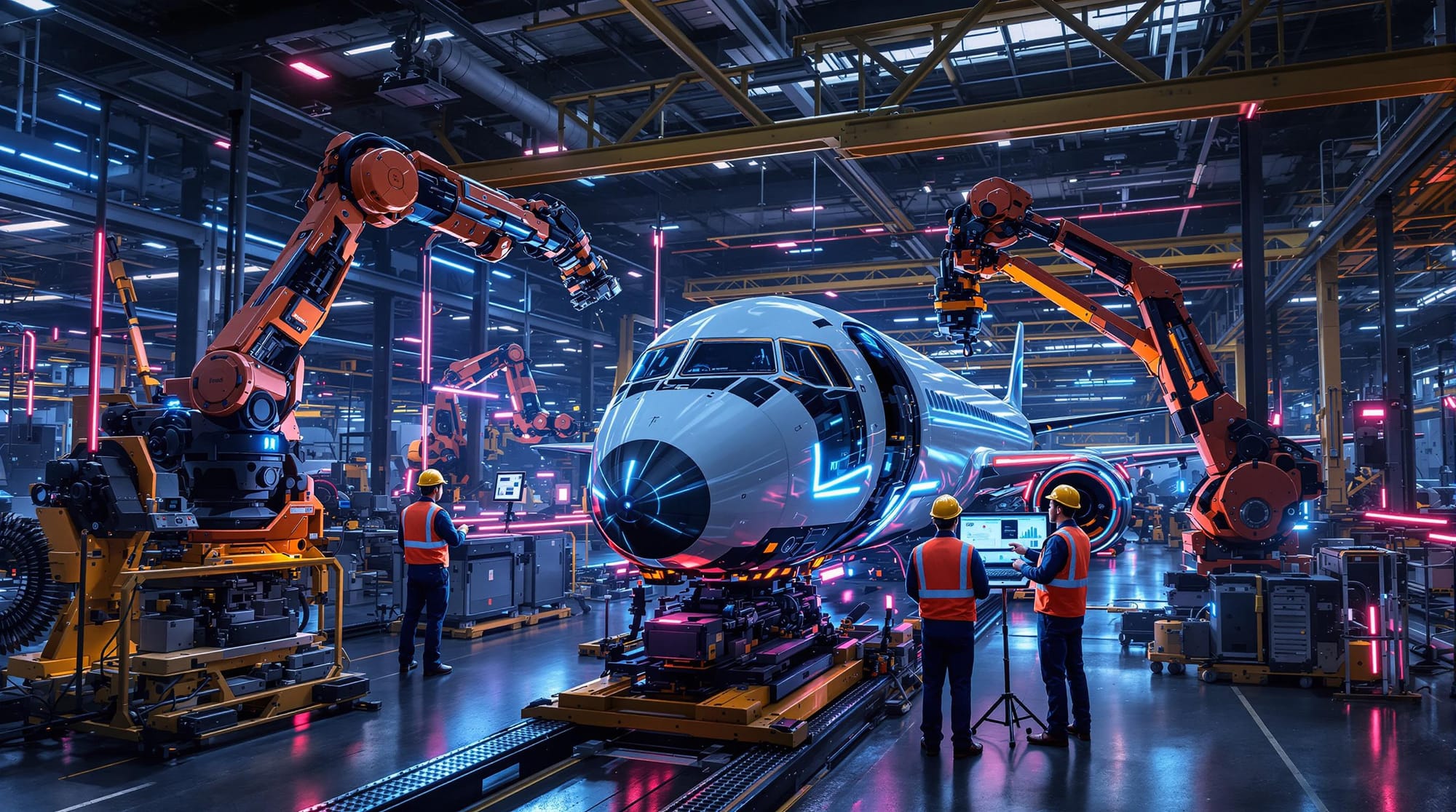
AI revolutionizes aerospace and defense manufacturing by solving critical challenges like supply chain delays, workforce shortages, and quality control inefficiencies. Here's how:
- Faster Production: AI tools reduce downtime and optimize workflows, improving efficiency.
- Enhanced Quality Control: Computer vision systems detect defects faster and more accurately than humans.
- Smarter Maintenance: Predictive maintenance minimizes equipment failures and costly downtime.
- Streamlined Supply Chains: Real-time monitoring and analytics improve supplier performance and inventory management.
- Innovative Design: Generative AI enables engineers to test thousands of designs, cutting costs and improving performance.
For example, Airbus reduced engineering prediction times from one hour to 30 milliseconds using AI, while Rolls-Royce uses digital twins to optimize engine performance. Ready to integrate AI into your processes? Start by identifying bottlenecks, building solid data systems, and testing small pilot projects.
Optimize Industrial Processes with Machine Learning
AI Technologies in Manufacturing
Aerospace and defense manufacturers are increasingly using AI systems to reshape production processes. These tools are changing how maintenance and quality control are handled, improving efficiency and precision.
Machine Learning for Equipment Maintenance
Machine learning is revolutionizing maintenance by analyzing large volumes of sensor data to predict equipment failures before they happen. This predictive method helps aerospace companies reduce expensive downtime.
Boeing’s "AnalytX" platform is a prime example, offering real-time insights for maintenance planning [2]. Similarly, Disney Aviation Group uses predictive maintenance to streamline fleet scheduling [1].
"The technology is there and the industry is ready... There have already been great strides within the industry to move toward the future." - Fern Campos, Aviation Director of Maintenance, Disney Aviation Group [1]
Computer Vision Inspection Systems
AI-driven computer vision systems are making quality control faster and more precise. These systems can spot defects that human inspectors might miss, ensuring better compliance and product standards.
The results have been impressive. For instance, some tools have cut engine inspection times by up to 90% [3]. Key features of these systems include:
- Object detection
- Instance segmentation
- Oriented bounding box (OBB) detection
- Real-time surface analysis
Manufacturers also integrate computer vision with drones to inspect hard-to-reach aircraft areas, capturing high-resolution images for detailed reviews [3].
Digital Twin Production Models
Digital twin technology is one of the most impactful AI applications in aerospace manufacturing. These virtual models allow manufacturers to test and refine processes before physical implementation. Rolls-Royce, for example, creates detailed digital twins of its engines, running them alongside physical systems to ensure accuracy [4].
"Digital twins become even more powerful in manufacturing. I can understand what the most efficient way to build a factory is by building a digital twin." - Todd Tuthill, vice-president for aerospace and defence, Siemens Digital Industries Software [4]
Real-world examples highlight the benefits of digital twins:
- General Motors cut costs by 95% using Synopsys Saber™ for virtual manufacturing instead of physical testing [5].
- PhysicsX worked with an aero-engine supplier to reduce waste from 30,000 quarantined parts annually using AI-based performance prediction models [4].
- In collaboration with Natilus, Siemens developed a digital twin of an 85-foot wingspan aircraft, viewable in a hangar with Sony XR Head Mounted Display technology [4].
These advancements are reshaping aerospace manufacturing, laying the groundwork for AI-driven improvements in supply chain management, quality assurance, and design processes.
AI Applications in Aerospace Manufacturing
AI is making waves in aerospace manufacturing, helping companies tackle challenges and improve efficiency in critical areas.
Supply Chain Management with AI
AI is changing how aerospace manufacturers handle supply chains. For example, ePlaneAI uses XGBoost and Random Forest algorithms to streamline operations. These tools have helped reduce Aircraft on Ground incidents, flagged 37% of inventory as outdated, reached 95% accuracy in short-term demand forecasting, and boosted labor efficiency by 65% [6].
In addition to managing procurement and inventory, AI enhances quality assurance throughout manufacturing processes.
AI Quality Control Systems
AI inspection systems are raising the bar for precision in aerospace quality checks. Here are some real-world examples:
Company | AI Application | Results |
---|---|---|
Rolls-Royce | Engine sensor analysis | Lowered unscheduled maintenance and improved aircraft performance [7] |
Boeing | Automated inspection systems | Improved verification of component quality [7] |
While quality control sees major improvements, AI also drives innovation in component design.
Parts Design Using AI
Generative design fueled by AI allows engineers to test thousands of design possibilities while meeting stringent industry standards [8]. Airbus is a standout example, using generative design to create optimized aircraft partitions. This approach evaluates thousands of designs simultaneously, focusing on reducing weight and improving structural performance [8].
Additionally, physics-based AI speeds up development by reusing simulation data, delivering more accurate predictions, and reducing simulation times [8].
Steps to Add AI to Manufacturing
Manufacturers looking to integrate AI into their operations should follow a clear, step-by-step approach to maximize efficiency and quality control.
Finding Production Bottlenecks
Production bottlenecks can significantly impact overall equipment effectiveness (OEE). For instance, after introducing AI-driven monitoring systems, Avalign Technologies improved OEE by 25-30% across four facilities [9].
To pinpoint bottlenecks, manufacturers should focus on these areas:
Area to Analyze | Key Metrics to Monitor |
---|---|
Equipment Performance | Machine speed, age, capacity |
Labor Issues | Training levels, skill gaps |
Supply Chain | Supplier reliability, delivery times |
Quality Control | Defect rates, inspection times |
Once bottlenecks are identified, the next step involves building a reliable data infrastructure to tackle these challenges.
Setting Up Data Systems
A well-structured data system is the backbone of any AI implementation. For example, a leading consumer goods manufacturer unified seven legacy ERP systems using Palantir's Foundry. This created a digital twin that resulted in estimated annual savings of $100 million [11].
"Data ingestion, harmonization, engineering and governance are 90% of the work that goes into building an AI system. If you focus on the 10% and let go of the 90%, you're dead from the start. So build that foundation of data." - Sanjay Srivastava, chief digital strategist at Genpact [12]
Key steps for setting up data systems include:
- Using time series databases for efficient IoT data storage
- Implementing real-time monitoring tools
- Establishing data validation protocols
- Centralizing data in cloud storage systems
With a strong data foundation, manufacturers can move on to testing AI applications through smaller pilot projects.
Testing AI in Small Projects
Pilot projects are a practical way to test AI's potential in specific scenarios. For example, ThroughPut's AI platform reduced production downtime by 10% and increased productivity by 15% [10].
"You should not have the expectation that you'll deploy this thing and it will radically transform the business. It's a lengthy process that takes time." - Ganapathy Krishnan, VP of engineering at Flipkart [12]
Consider these best practices for pilot projects:
- Select focused use cases with measurable success criteria
- Secure executive support and allocate sufficient funding
- Build teams that combine technical and domain expertise
- Keep detailed records of testing processes and outcomes
- Start small - test on one facility or production line before scaling up
Next Steps for AI Manufacturing
AI adoption is transforming industries. For instance, a technology training incubator cut contact center response times from 24 to 6 hours and automated 80% of inquiries, resulting in $120,000 in annual savings [14].
Benefit Area | Typical Improvement |
---|---|
Production Efficiency | 5% boost, translating to millions in revenue [13] |
Quality Control | 13% rise in customer satisfaction scores (CSAT) [14] |
Cost Reduction | Over $100,000 saved annually [14] |
Examples like OTTera, which used data analytics to expand markets through better customer insights, and Waggel, which improved worker productivity by organizing data more effectively, highlight the transformative power of AI [14]. These results show how integrating AI can drive measurable improvements across operations.
Steps to Begin with AI
Manufacturers need a strong digital foundation to fully leverage AI. Only 30% of aerospace and defense companies use AI, with larger firms (with annual revenue of $10B+) leading the adoption [13].
Here’s how to get started:
- Assess Digital Readiness: Check if your manufacturing execution system (MES) can handle AI integration [13].
- Improve Data Quality: Build systems that ensure data is accurate, comprehensive, and easily accessible [13].
- Set Clear Goals: Define SMART objectives for each AI project [14].
- Prioritize Security: In 2022, 83% of manufacturing clients will have undocumented external connections, so it’s critical to implement data anonymization and multi-factor authentication before deploying AI [15].
- Track Metrics: Measure progress using qualitative and quantitative indicators [14].
"Organizations should proactively create avenues for employees to upskill with AI and reframe the narrative to not fear AI and the unknown but to showcase what's possible - their workforce leading, adapting, and adding unprecedented value." - Matthew Daniel, senior principal for talent strategy at Guild [16]
Related Blog Posts
- Why Supply Chains Are Still Chaos for Manufacturers
- Boom Supersonic: Pioneering the Future of High-Speed Aviation
- Microsoft's Majorana 1 Quantum Chip - Strategic Implications for Enterprise Adoption and Market Dynamics
- Space Race 2.0: How the U.S., China, and Private Companies Are Shaping the New Frontier