American Dynamism: Why Tech Is Rebuilding U.S. Industry
Explore how technology is transforming U.S. industries, enhancing efficiency, and reshaping the workforce in manufacturing, defense, and energy.
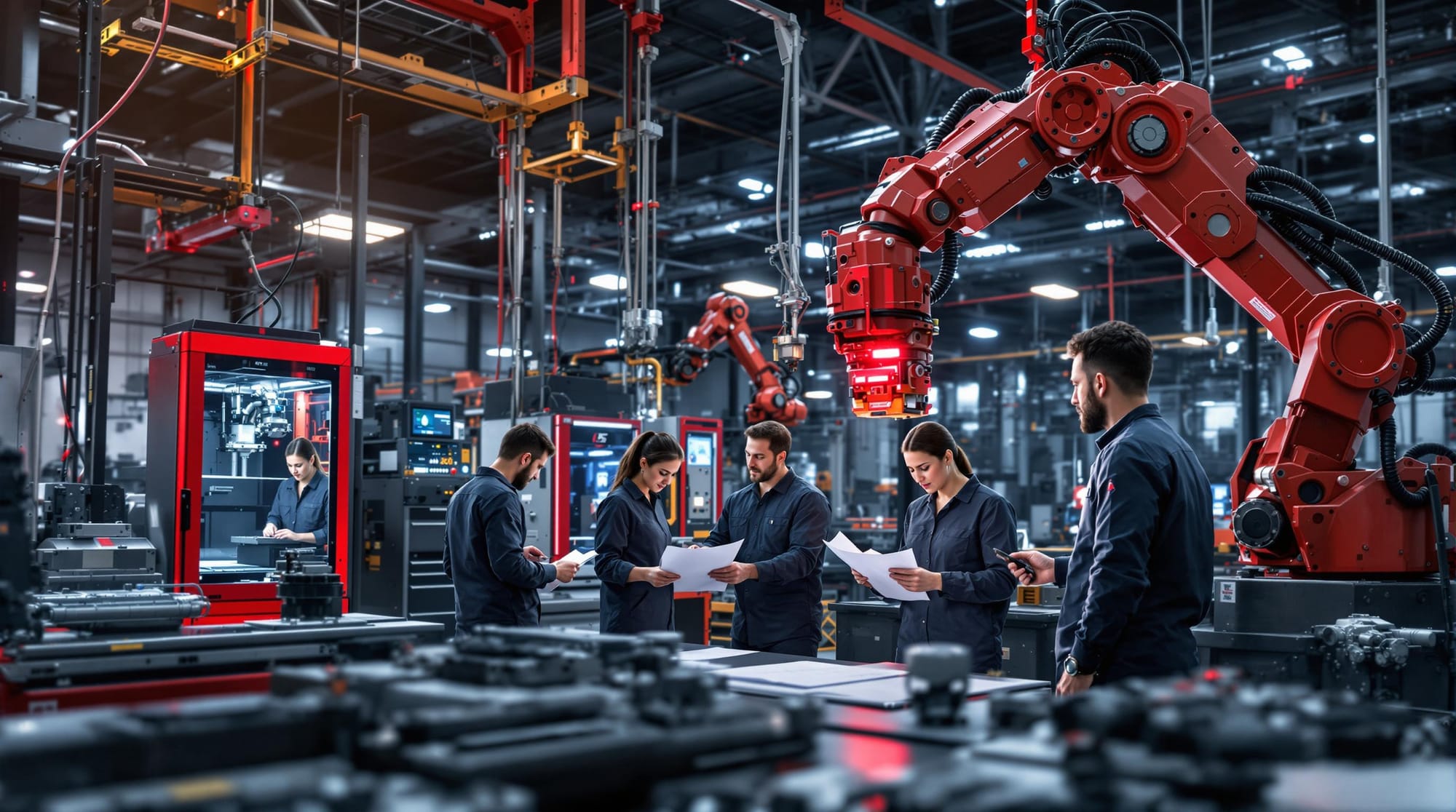
Technology is reshaping U.S. industries, driving manufacturing, defense, and energy growth while addressing supply chain issues, cybersecurity threats, and workforce challenges. Here’s what you need to know:
- Key Challenges: Supply chain disruptions, cybersecurity risks (the average data breach cost in 2023 was $4.45M), and skilled labor shortages affect over 71% of companies.
-
Tech Solutions:
- AI: Cuts manufacturing costs by 72% and speeds up production.
- 3D Printing: Reduces costs and improves efficiency in aerospace, defense, and aviation.
- Energy Systems: Investments in battery storage and CO2 capture are reducing emissions and costs.
- Connected Systems: IoT and digital twins optimize operations and reduce emissions.
-
Leading Companies:
- SpaceX: Lowering space travel costs with reusable rockets.
- Anduril: Advancing defense with AI-driven systems.
- Boom Supersonic: Building sustainable supersonic aircraft with major economic impact.
- Workforce Impact: Automation is creating new high-skill jobs, but it could leave a 1.9 million-worker gap by 2033. Retraining programs and STEM education are critical.
- Economic Growth: Manufacturing is strengthening U.S. GDP, reducing reliance on foreign suppliers, and modernizing traditional industrial hubs.
Takeaway: Advanced technology is revitalizing U.S. industries, improving efficiency, creating high-paying jobs, and boosting economic resilience. However, workforce retraining, energy demands, and regulatory compliance remain key challenges.
Key Technologies Changing U.S. Industry
AI in Factory Operations
AI is reshaping U.S. manufacturing, with the market valued at $1.1 billion in 2023 and expected to grow by 16.7% annually through 2029 [1]. Major manufacturers have reported a 72% drop in operational costs after adopting AI systems [2].
AstraZeneca has leveraged AI to cut lead times by half and reduce active ingredient usage by 75%, turning manufacturing timelines from weeks into hours [3].
"Today, AstraZeneca is using AI to revolutionize how we develop, make and supply medicines." - Jim Fox, Vice President Sweden Operations and Executive Sponsor for Digital, AstraZeneca [3]
This efficiency level is paving the way for even more advancements in energy and production technologies.
New Energy Systems
The manufacturing sector is also experiencing a surge in battery storage investments, which grew by over 20% in 2024 and crossed $50 billion. At the same time, lithium-ion battery costs dropped another 40% in 2024, continuing a decade-long 90% price reduction [4].
In Texas, the Valero Refinery in Port Arthur has achieved impressive results with Air Products' CO2 capture technology, reaching over 90% efficiency. This process purifies CO2 streams from 10-20% to over 97% [5].
3D Printing and Smart Factories
3D printing is driving cost savings and efficiency improvements across various industries:
Industry | Application | Results |
---|---|---|
Aviation | Lufthansa Technik's custom nozzle production | 72 nozzles per print run, cutting costs [6] |
Defense | French Army's spare parts program | 50 printers deployed, speeding up supply chains [7] |
Aerospace | AMRC's drilling cap production | 250 caps made in 2 days, compared to weeks [6] |
These advancements are strengthening the foundation of the U.S. industrial sector.
Connected Industry Systems
Digital twins and IoT are helping companies like Jubilant Ingrevia reduce process variability by 63%, cut costs, and lower Scope 1 emissions by 20% [3].
Mengniu Dairy has seen a 73% boost in inventory turnover and an 8% rise in operational efficiency thanks to AI-powered supply chain systems [3].
"Through the integration of AI-driven innovations, we have not only optimized our manufacturing processes and design but also empowered our workforce." - Nihat Bayiz, Chief Production and Technology Officer, Beko [3]
These connected technologies are forming a solid framework for the ongoing transformation of U.S. industries.
Inside the Future of American Manufacturing
Companies Leading Industrial Change
As new technologies reshape industries, certain companies are driving this wave of transformation.
SpaceX: Reducing Space Travel Costs
SpaceX has made space launches more affordable with its Falcon 9 rocket, offering payload delivery to orbit for $62 million per launch. This brings costs down significantly - from over $200 million to around $2,700–$3,000 per kilogram to Low Earth Orbit (LEO) [8][9]. In October 2024, the company achieved another milestone when its Starship and Super Heavy Booster performed a "chopstick catch", returning directly to the launch tower and cutting transportation costs [9].
"Reusable rockets are poised to transform the space industry by bringing about profound, game-changing benefits in cost efficiency, sustainability and technological advancement." - Global Aerospace [9]
Anduril: Advancing Defense with AI
Anduril Industries, valued at $14 billion [11], is reshaping defense technology through artificial intelligence. In December 2024, it partnered with OpenAI to improve counter-unmanned aircraft systems (CUAS), enhancing data processing and situational awareness [10].
The company’s AI-driven operating system, Lattice, enables autonomous capabilities for defense missions. With Lattice Mesh, Anduril has opened its software infrastructure to other companies, allowing data sharing and collaboration [11].
"Our partnership with OpenAI will allow us to utilize their world-class expertise in artificial intelligence to address urgent Air Defense capability gaps across the world. Together, we are committed to developing responsible solutions that enable military and intelligence operators to make faster, more accurate decisions in high-pressure situations." - Brian Schimpf, co-founder & CEO of Anduril Industries [10]
Boom Supersonic: Revolutionizing Aviation
Boom Supersonic is changing the aviation landscape with its Overture Superfactory in Greensboro, NC [12].
Metric | Value |
---|---|
Annual Production Capacity (First Line) | 33 aircraft ($6+ billion value) [12] |
Planned Full Capacity | 66 aircraft annually [12] |
Economic Impact (NC, 20 years) | $32.3 billion [12] |
Direct Jobs Created | 2,400+ positions [12] |
Current Order Book | 130 aircraft [12] |
In March 2024, Boom's XB-1 demonstrator aircraft earned FAA approval for supersonic flight testing in Mojave, California [12].
"Construction of the Overture Superfactory represents a major milestone toward ensuring the United States' continued leadership in aerospace manufacturing. Supersonic flight will transform air travel, and Overture provides a much-needed innovative alternative for airlines across the globe." - Blake Scholl, founder and CEO of Boom Supersonic [12]
Boom is also focusing on reducing environmental impact. The Overture aircraft is designed to run entirely on sustainable aviation fuel (SAF), to achieve net-zero carbon emissions by 2025 [13]. The company has already secured commitments for 10 million gallons of SAF annually for its flight test program [14].
Effects on U.S. Economy and Security
Changes in Industrial Jobs
The tech boom in U.S. manufacturing is reshaping the workforce. By 2033, industries may face a gap of 1.9 million workers [15] as manual labor gives way to roles requiring advanced skills due to automation and cutting-edge machinery.
Certain roles are expected to see notable growth:
Role Type | Growth by 2032 | Key Skills Required |
---|---|---|
Industrial Machinery Technicians | 16% | Equipment maintenance, digital systems |
Software/Web Developers | 13% | Programming, systems integration |
Data Scientists | 30% | Analytics, machine learning |
In the automotive industry, robots now handle 38% of manufacturing tasks, reducing traditional labor roles by 14%. However, this shift creates new positions for skilled technicians and engineers [16]. These changes are setting the stage for a manufacturing revival centered around innovation.
U.S. Manufacturing Power
The U.S. economy is showing signs of manufacturing strength alongside these workforce changes. Real GDP grew by 2.3% in the fourth quarter of 2024, following a 3.1% increase in the prior quarter [17].
A major driver of this resurgence is the push to reduce reliance on foreign supply chains. For example:
- The Navy cut its use of Chinese suppliers for critical technologies by 40% in 2023 [19].
- The Army reduced its dependence on Chinese suppliers by 17% from 2022 to 2023 [19].
"We know we're never going to get China fully out of U.S. supply chains. That's not even the goal, but managing the presence of lots of different foreign suppliers and aligning those to the right level of capability or component or parts, making sure we have redundancy where we need it and that the most sensitive parts are fully protected and coming either directly from the United States or from friends and allies is really what the call to action is." - Tara Murphy Dougherty, Govini's chief executive officer [19]
New Industrial Cities
Traditional manufacturing hubs are evolving into tech-industrial centers, reflecting the tech-driven transformation of the U.S. industry. Companies are responding with strategies like flexible work schedules, housing and commuting support, targeted training programs, and advanced workplace technologies.
Despite progress, challenges remain. Around 68% of worker separations in the sector are due to voluntary quits [18]. Companies are focusing on creating better work environments and career growth opportunities to address this. This is especially critical in aerospace and defense, where retaining skilled workers is essential for national security [18].
Problems and Solutions
As American Dynamism reshapes U.S. industries, tackling challenges in workforce development, energy consumption, and regulatory compliance remains a top priority.
Job Training Needs
By 2030, an estimated 375 million workers - about 14% of the global workforce - will need to retrain as automation reshapes jobs in manufacturing, assembly lines, and data entry roles [20].
The urgency of this issue is reflected in the following:
Issue | Effect | Industry Response |
---|---|---|
Skills Gap | 62% of executives anticipate retraining or replacing over 25% of their workforce by 2023 | Launch targeted training programs |
Preparedness | Only 16% of business leaders feel "very prepared" | Focus on skill mapping |
Annual Impact | 20 million unemployment events in a typical year | Develop transition support systems |
"McKinsey Global Institute warns that few precedents exist for retraining vast workforces" [21].
While workforce retraining is critical, industries must address energy and regulatory hurdles to ensure long-term resilience.
Safety and Energy Issues
The energy demands of U.S. industries drive emissions and are expected to grow significantly. If left unchecked, energy demand could rise by 30% by 2050, leading to a 17% increase in emissions [22].
Efforts to improve energy efficiency are yielding results:
- Manufacturing facilities waste an estimated 7 quadrillion British thermal units of thermal energy annually [22].
- Products that improve building efficiency generate $60 billion in U.S. revenue, a 43% increase over four years [23].
- The Advanced RTU Campaign has saved 2 trillion kWh and reduced CO2 emissions by 758 million pounds [23].
Better Industry Rules
Modernizing industry regulations is just as important as retraining and energy efficiency. Increased regulatory scrutiny impacts tech companies, with the ten largest GDPR fines totaling approximately $4.1 billion [25]. Adobe's failed $20 billion Figma acquisition in 2023 highlights the influence of regulatory decisions [25].
"Compliance capabilities have to be integrated into a tech company's thinking, which is not easy" [25].
To navigate this shifting landscape, companies should:
- Establish internal compliance standards
- Implement robust monitoring systems
- Conduct thorough risk assessments
- Build strong relationships with regulators
"A fluid regulatory environment gives organizations an opportunity to influence regulations and modernize their approaches to compliance for enhanced effectiveness and cost efficiencies" [24].
Conclusion: The New American Industry
Tech's Impact on Industry
Technology has transformed U.S. manufacturing in remarkable ways. Over the last two decades, worker productivity has jumped by 47%, and industrial robots have surged from 1.2 million in 2013 to a projected 1.9 million units. The U.S. also accounts for 28% of global R&D spending, highlighting its position as an industrial leader [27]. Automation, in particular, has led to a 16% reduction in labor costs [26].
Shifts in labor patterns reflect the growing role of automation across industries:
Metric | Current Status | Industry Impact |
---|---|---|
Manufacturing Jobs | 8% of workforce (down from 14% in 1996) | Fewer roles due to automation |
Vacant Positions | 55% of manufacturing roles | Skills gap challenges |
Employee Turnover | 40% average rate | Workforce instability |
These advancements highlight the need for ongoing investment and supportive policies to maintain industrial leadership.
Next Steps
To sustain and expand these gains, all stakeholders must take action:
- Manufacturing companies should focus on integrating technologies like data analytics, 3D printing, and smart factory systems. Success lies in collaborating with technology rather than resisting it [28].
- Educational institutions must emphasize STEM education as the traditional career model evolves into lifelong learning [28]. Training programs must be redesigned to equip workers with the skills needed for modern industry roles.
- Government agencies should prioritize strengthening digital infrastructure, updating competition policies, and aligning labor regulations with technological advancements [28][29]. Effective governance will ensure that smart machines and emerging technologies are supported by practical, forward-looking policies [29].
The future of American manufacturing rests on how well we integrate technological progress with workforce development and regulatory updates. By doing so, the U.S. can continue to lead in this new industrial era.